Студенты журфака УРФУ вместе с журналистами «Областной газеты» побывали в самом сердце фарфорового производства и увидели, как из жидкой массы родился «бумажный» кораблик. В формовочном цехе предприятии «Фарфор Сысерти» льют, сушат, склеивают, вытачивают разрисовывают вручную не просто предметы, а настоящие произведения ремесленного искусства.
«Вот видите эти трубы? — показывает начальник формовочного цеха № 1 Татьяна Хасанова. — По ним шликер поступает к рабочим местам. На конце каждого шланга — кран. Рабочий подставляет гипсовую форму, открывает кран — и заливает фарфоровую массу».
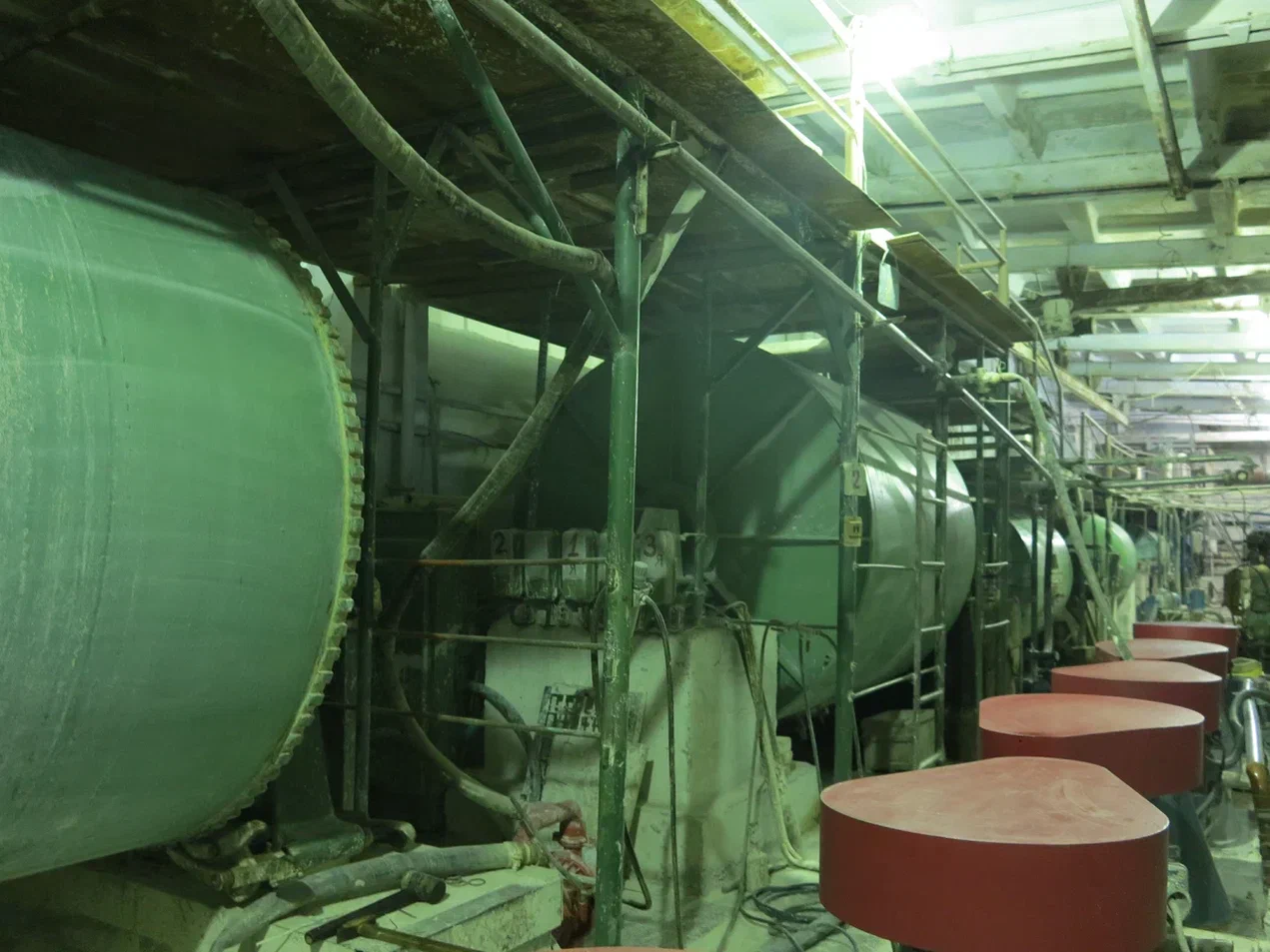
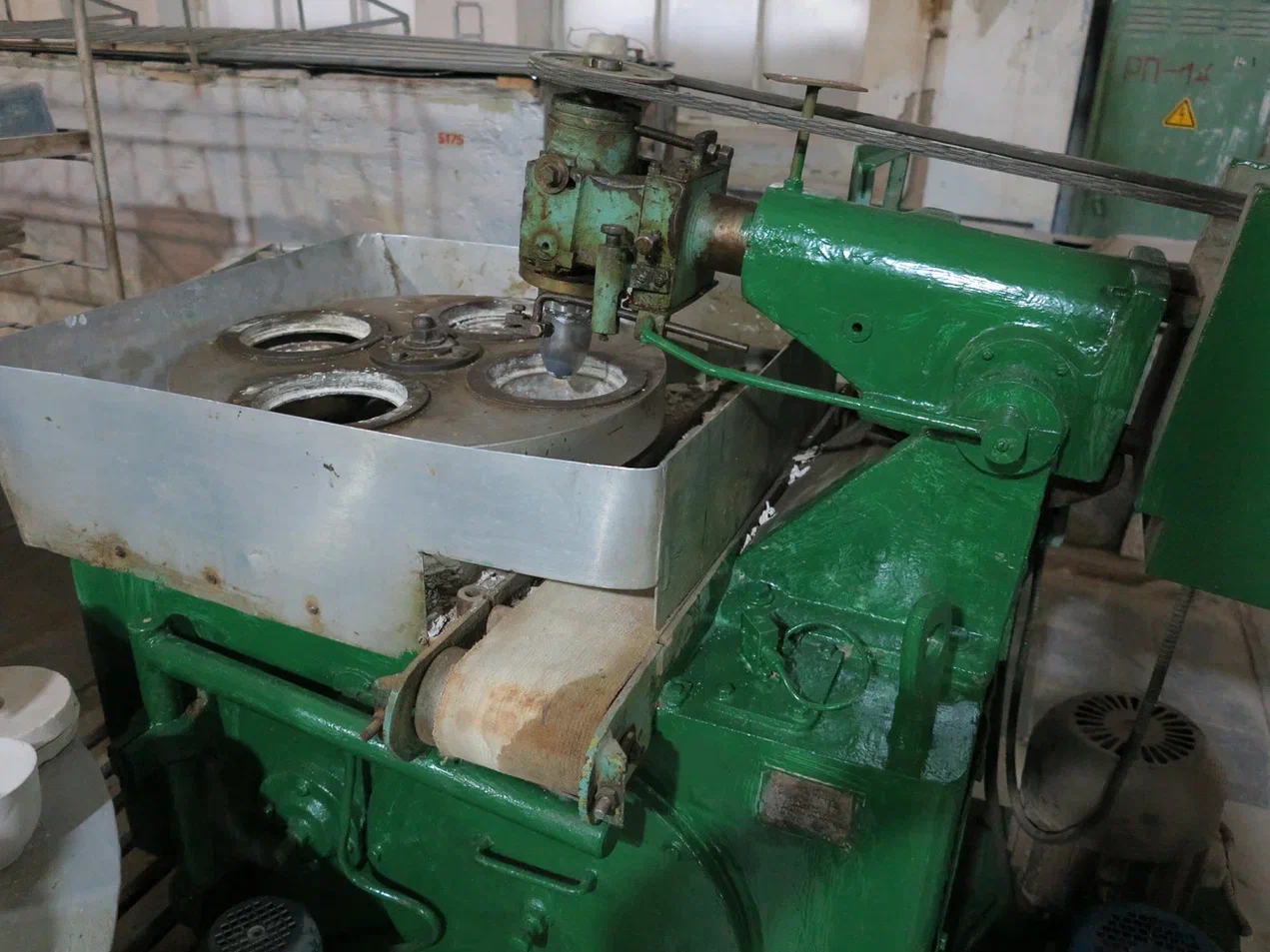
Работа начинается задолго до заливки. Сначала готовят сам шликер — фарфоровую массу, в состав которой входят каолин, серая глина, кварцевый песок и полевой шпат. Всё это перемешивается с водой, а затем очищается.
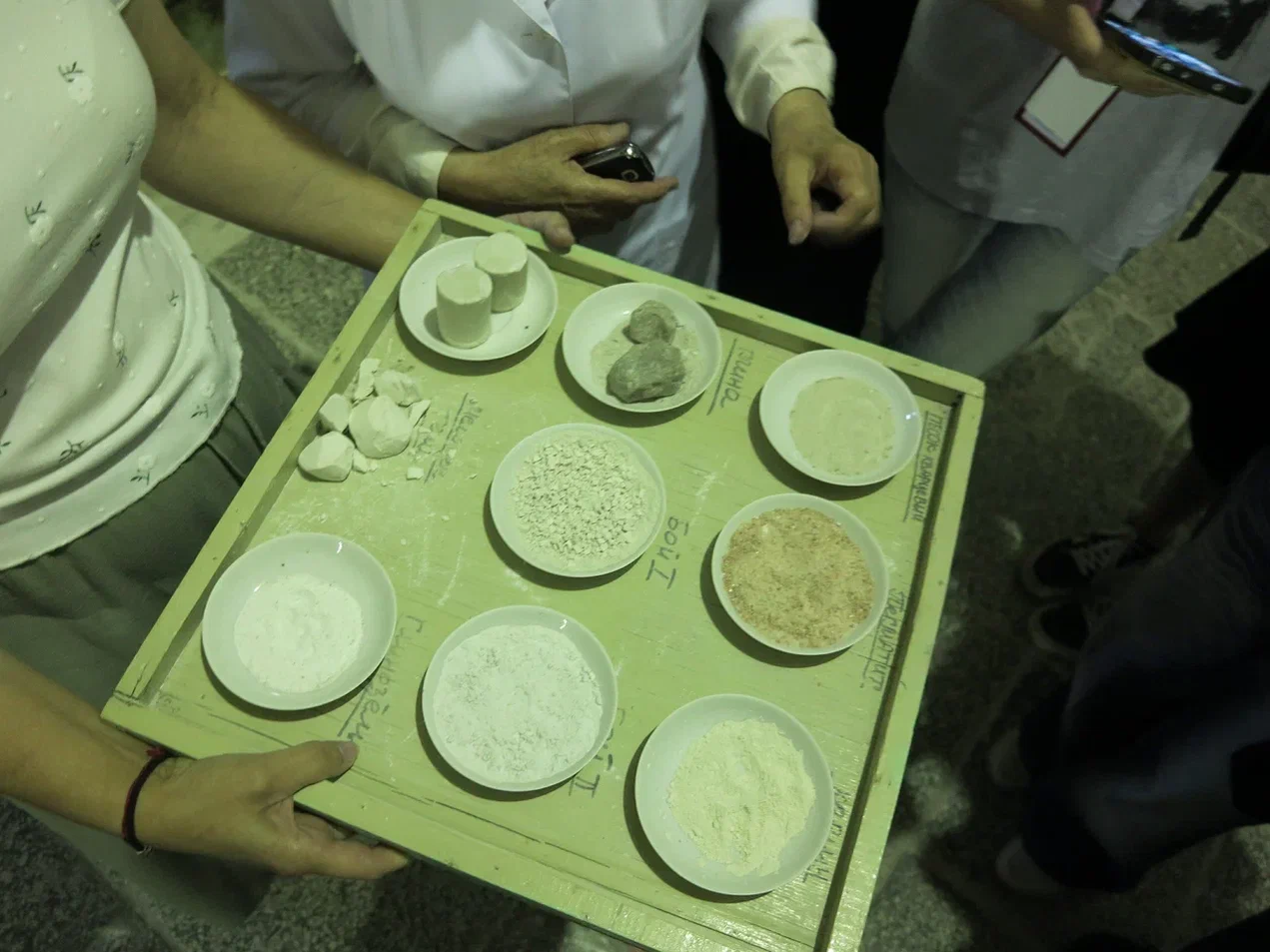
«Мы убираем из массы все лишнее — комочки, железо, — рассказывает Татьяна Хасанова. — Представляете, на магнитах прямо слой образуется. Каждые 10–15 минут приготовитель масс проверяет и промывает систему».
Затем масса поступает в цех — и начинается формовка. Жидкий шликер заливается в гипсовые формы, которые впитывают влагу, а глина оседает по стенкам, образуя так называемый черепок — заготовку будущего изделия.
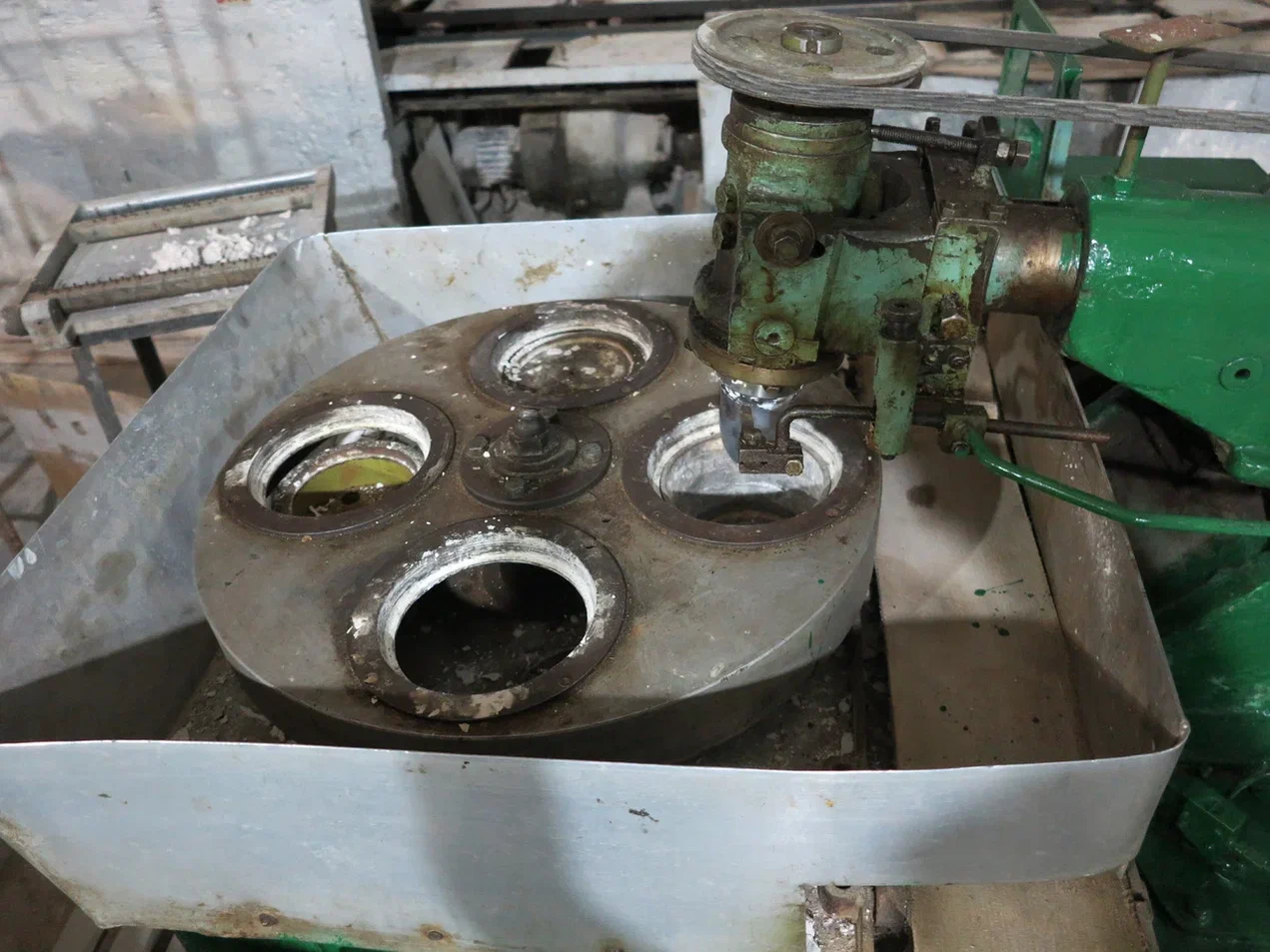
«У каждого формовщика — набор форм. Он сам отслеживает время, сливает излишки, потом подрезает летник и отправляет изделие на сушку», — объясняет начальник цеха.
Работа здесь требует не только внимания, но и настоящего мастерства. Ведь большинство изделий сложной формы состоят из нескольких частей, которые нужно соединить вручную. «Вот, например, чайник: сначала делаем корпус, потом приклеиваем носик, ручку. Даже дырочки под носик — вручную. Всё это после обрезки и сушки», — улыбается Татьяна Николаевна.
Отдельное направление — изделия из густой фарфоровой массы. Для плоских предметов, таких как тарелки или блюдца, используют пресс-формовку. Специальные станки формуют «колбаску» из плотной массы, которую вручную закладывают в форму, затем изделие вращается, приобретая нужную толщину. «Ролик задаёт толщину и даже может сформировать кольцо жёсткости — это то, чего не добьёшься в литье», — поясняет технологию Татьяна Хасанова.
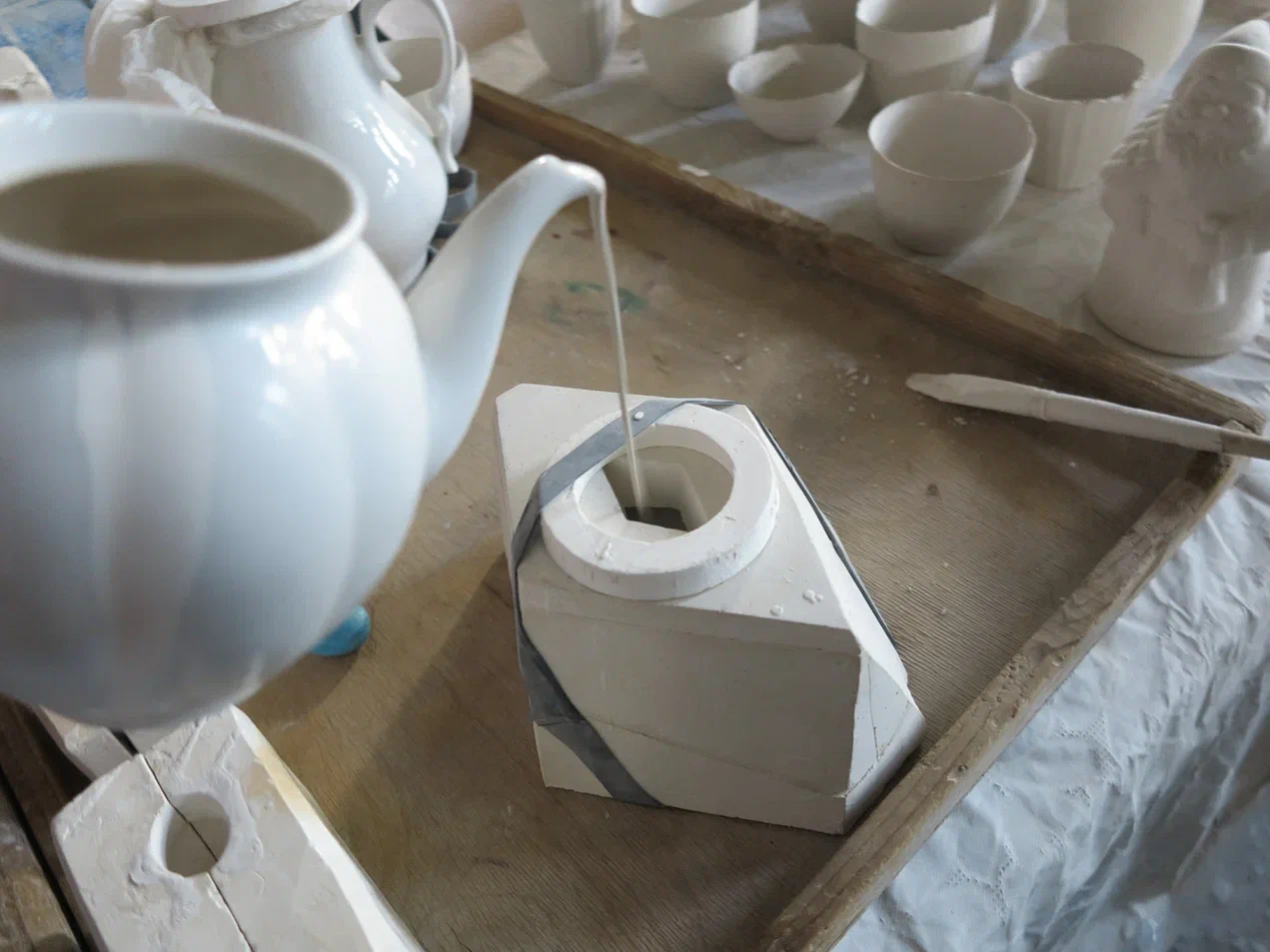
После формования изделия проходят сушку при температуре 55 градусов.
Когда влажность снижается до 2–4%, детали соединяются, зачищаются, продуваются воздухом и только после этого идут на обжиг. «Сейчас вы видите шов — его замывают, потом проверяют у контролёра. Только тогда можно обжигать», — показывает специалист.
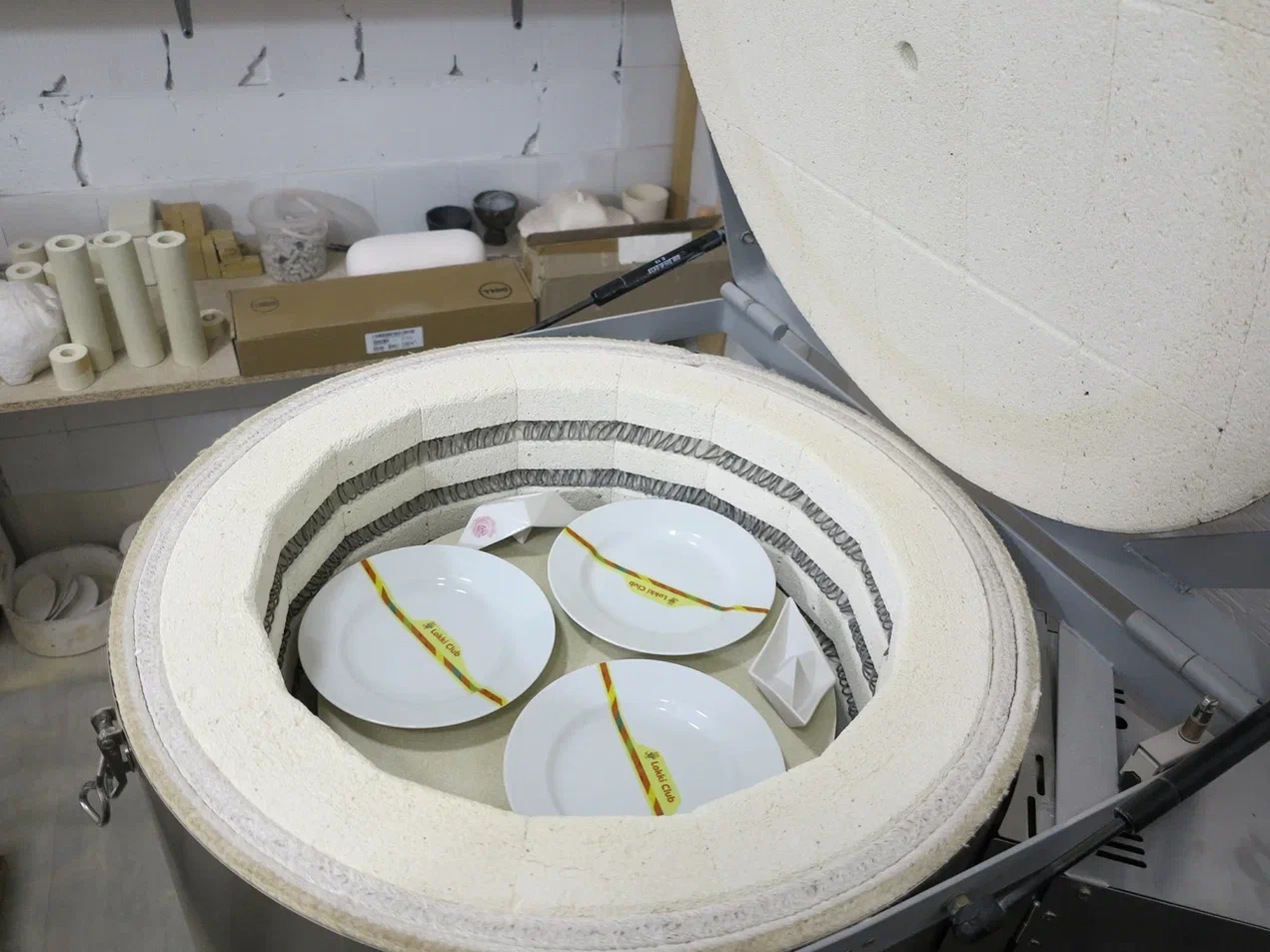
Любопытная деталь: часть бракованных или повреждённых изделий здесь не утилизируют, а выкладывают на специальный стол — для туристов. Каждый гость фабрики может вживую увидеть процесс рождения фарфора. А если повезёт, и самому поучаствовать в мастер-классе.
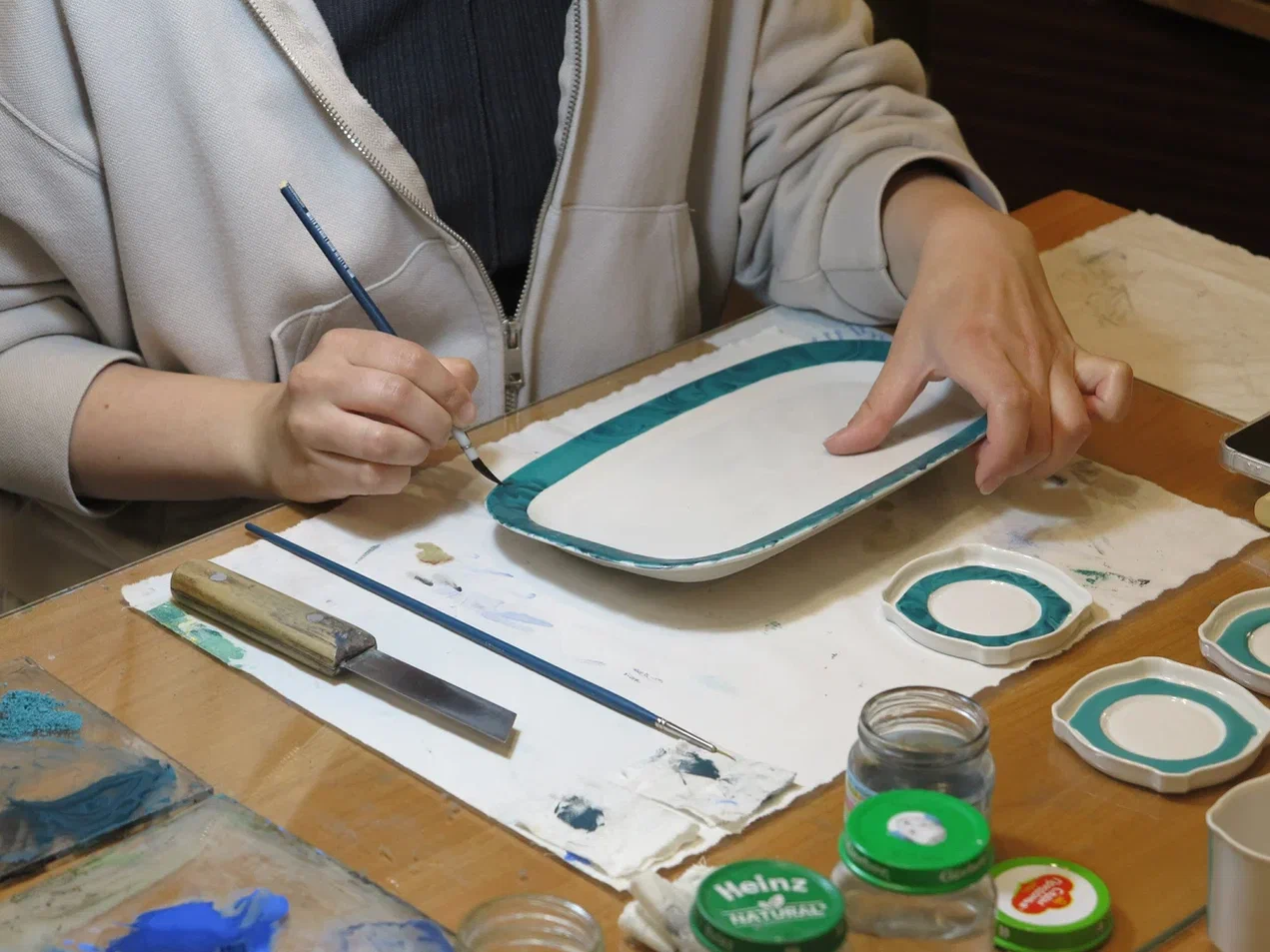
«Фарфор Сысерти» — это не просто производство, а живое искусство. Здесь каждый чайник проходит через руки мастера, а каждая чашка хранит в себе тепло гипсовой формы, терпение формовщика и чуть-чуть магии. Той самой, уральской.
Ранее «Областная газета» писала о том, что в Сысерти к юбилею издания создали символ «Областной газеты» — фарфоровый кораблик.
Алина Гилязова